Animal feed milling machines play a crucial role in the production of high-quality feed for livestock and poultry. A 5 t/h machine is suitable for small to medium-scale operations, providing an efficient and cost-effective solution for feed production. When selecting a 5 t/h animal feed milling machine, choosing the right components is essential for ensuring optimal performance, durability, and efficiency. This article explores the key components of a 5 t/h animal feed milling machine and provides guidance on how to select them.
1. Electric Motor
The electric motor is the primary power source for the feed milling machine. Selecting the right motor is crucial for ensuring efficient operation and minimizing energy consumption.
- Power Rating: Choose a motor with sufficient power to drive the machine at its rated capacity. Typical motors for a 5 t/h machine range from 30 to 45 kW, depending on the specific design and components.
- Energy Efficiency: Select an energy-efficient motor, such as a premium efficiency or IE3 class motor, to reduce energy costs and environmental impact.
- Brand and Quality: Choose a reputable motor brand known for quality and reliability, such as Siemens, ABB, or WEG. High-quality motors have longer lifespans and require less maintenance.
2. Hammer Mill
The hammer mill is responsible for grinding raw materials into fine particles, preparing them for further processing. Selecting the right hammer mill is critical for achieving consistent particle size and efficient feed production.
- Rotor Design: Choose a hammer mill with a well-designed rotor that ensures even distribution of materials and minimizes wear on the hammers and screen.
- Screen Size: Select a screen size appropriate for the type of feed being produced. Typical screen sizes for a 5 t/h machine range from 2 to 4 mm, depending on the feed formulation.
- Material and Construction: Opt for a hammer mill made from high-quality materials, such as hardened steel or alloy, to ensure durability and resistance to wear.
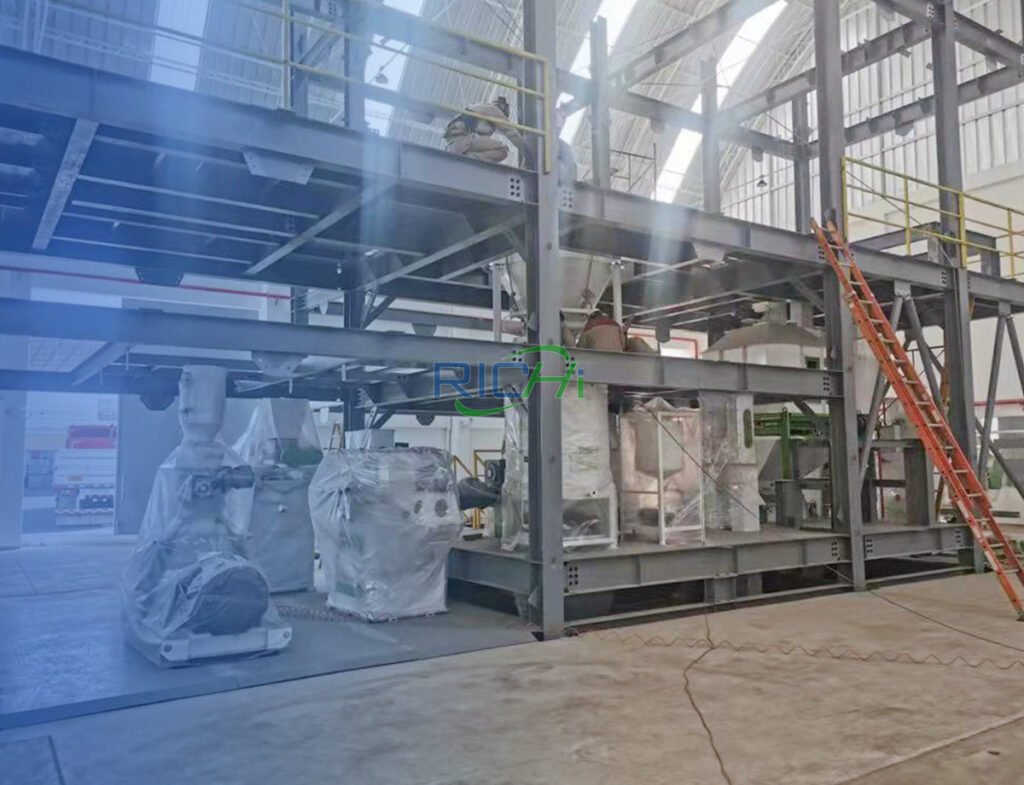
3. Mixer
The mixer is responsible for blending raw materials and additives to create a homogeneous feed mixture. Selecting the right mixer is essential for ensuring consistent feed quality and nutritional value.
- Mixing Capacity: Choose a mixer with a capacity suitable for your production needs. For a 5 t/h machine, a mixer with a capacity of 1 to 2 tons is typically sufficient.
- Mixing Action: Select a mixer that provides efficient and uniform mixing, such as a horizontal or vertical ribbon mixer. The mixing action should ensure that all ingredients are thoroughly blended.
- Material and Construction: Choose a mixer made from materials that are resistant to corrosion and wear, such as stainless steel or coated mild steel.
4. Pellet Mill
The pellet mill is the heart of the feed milling machine, responsible for compressing the feed mixture into pellets. Selecting the right pellet mill is crucial for achieving high-quality pellets and efficient production.
- Die Size: Choose a die size appropriate for the type of feed being produced. Typical die sizes for a 5 t/h machine range from 4 to 6 mm, depending on the feed formulation.
- Roller Configuration: Select a pellet mill with rollers that are designed to provide even pressure and distribution of materials across the die surface.
- Material and Construction: Opt for a pellet mill made from high-quality materials, such as hardened steel or alloy, to ensure durability and resistance to wear.
5. Cooler and Screener
The cooler and screener are responsible for cooling and sifting the pellets after they exit the pellet mill. Selecting the right cooler and screener is essential for ensuring consistent pellet quality and efficient production.
- Cooling Capacity: Choose a cooler with a capacity suitable for your production needs. For a 5 t/h machine, a cooler with a capacity of 5 to 6 tons per hour is typically sufficient.
- Screening Efficiency: Select a screener that provides efficient sifting of the pellets, removing any fines or oversize particles.
- Material and Construction: Choose a cooler and screener made from materials that are resistant to corrosion and wear, such as stainless steel or coated mild steel.
6. Control System
The control system is responsible for monitoring and controlling the operation of the feed milling machine. Selecting the right control system is essential for ensuring efficient operation and minimizing downtime.
- Automation Level: Choose a control system with an appropriate level of automation for your needs, ranging from basic manual controls to advanced PLC-based systems.
- User Interface: Select a control system with a user-friendly interface that provides clear and intuitive information about the machine’s operation.
- Reliability: Choose a control system from a reputable manufacturer known for quality and reliability, such as Siemens, Allen-Bradley, or Schneider Electric.
7. Maintenance and Support
When selecting components for a 5 t/h animal feed milling machine, it’s important to consider the availability of maintenance and support services.
- Spare Parts: Choose components from manufacturers that offer readily available spare parts, ensuring that any necessary repairs can be made quickly and efficiently.
- Technical Support: Select manufacturers that provide comprehensive technical support, including on-site service, remote troubleshooting, and training for operators and maintenance personnel.
Conclusion
Selecting the right components for a 5 t/h animal feed making machine is essential for ensuring optimal performance, durability, and efficiency. By choosing high-quality components from reputable manufacturers and considering factors such as power rating, material and construction, and maintenance and support, feed producers can ensure that their machine operates at peak performance and delivers consistent, high-quality feed. By investing in the right components, feed producers can enhance their productivity, reduce operating costs, and stay competitive in the rapidly evolving animal feed market.