The global transition toward renewable energy sources has led to a significant rise in demand for wood pellets. However, countries with stringent environmental protection standards profoundly impact the design and operation of wood pellet production lines. This article examines how these rigorous regulations shape the engineering, equipment selection, and operational practices within wood pellet manufacturing facilities.
Key Environmental Issues in Wood Pellet Production
- Air Emissions
The production of wood pellets can release particulate matter, volatile organic compounds (VOCs), and greenhouse gases. Countries with strict environmental regulations often mandate advanced emission control systems. - Water Usage and Wastewater Management
Water is frequently used in production processes for cooling and steam generation. Stringent regulations necessitate efficient water usage and the proper treatment of wastewater. - Noise Pollution
Industrial operations can generate considerable noise. Environmental regulations may impose limits on noise levels, influencing equipment selection and facility design. - Waste Management
Proper handling and disposal of waste materials, including wood dust and rejected pellets, are crucial aspects regulated by environmental laws. - Energy Efficiency
Many countries with strict environmental standards also emphasize energy efficiency in industrial processes.
Countries with Stringent Environmental Regulations
Several countries are recognized for their rigorous environmental protection requirements, significantly impacting wood pellet production line design:
- Germany
- Sweden
- Netherlands
- Denmark
- United States (especially California)
- Canada
- Japan
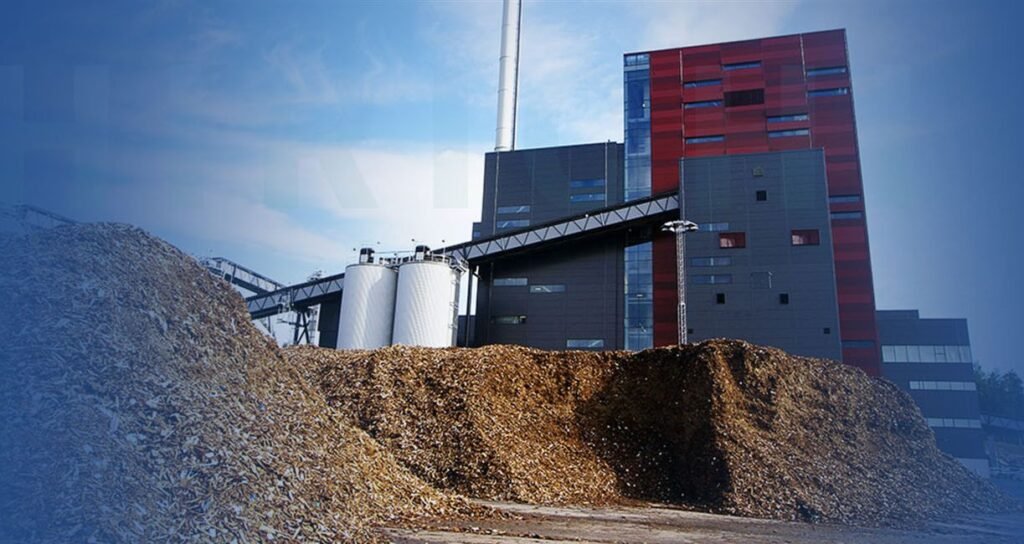
The Impact of Strict Regulations on Production Line Design
- Advanced Emission Control Systems
In countries with stringent air quality regulations, wood pellet production lines must incorporate sophisticated emission control technologies:- Cyclones and Baghouses: Essential for capturing particulate matter, high-efficiency cyclones and fabric filter baghouses are often required to meet strict particulate emission limits.
- Regenerative Thermal Oxidizers (RTOs): To control VOC emissions, RTOs may be necessary, achieving destruction efficiencies of over 99%.
- Wet Electrostatic Precipitators (WESPs): For ultra-fine particle control, WESPs may be integrated, especially in regions with very stringent particulate matter regulations.
- Water Management Systems
Countries with strict water conservation and quality regulations influence production line design through:- Closed-Loop Cooling Systems: Implemented to minimize water consumption, reducing both freshwater intake and wastewater discharge.
- Advanced Wastewater Treatment: On-site facilities may need to incorporate technologies like membrane bioreactors or advanced oxidation processes to meet discharge standards.
- Noise Reduction Measures
To comply with noise regulations, production line designs may include:- Acoustic Enclosures: Key equipment like hammer mills and pellet presses may be enclosed in sound-insulated housings.
- Silencers: Exhaust systems and pneumatic conveyors often require silencers to mitigate noise levels.
- Strategic Equipment Placement: Optimizing the layout of the production line to minimize noise impact on surrounding areas.
- Efficient Material Handling and Dust Control
Strict regulations on particulate emissions and worker safety necessitate advanced material handling and dust control systems:- Enclosed Conveyors: Enclosed belt or screw conveyors are often used to minimize dust emissions.
- Dust Collection Systems: Comprehensive networks are integrated throughout the production line, featuring strategically placed collection points.
- Spark Detection and Suppression: Advanced systems are implemented to prevent dust explosions.
- Energy-Efficient Equipment and Processes
Countries emphasizing energy efficiency in industrial processes influence production line design through:- High-Efficiency Motors: Using premium efficiency motors and variable frequency drives (VFDs) to optimize energy consumption.
- Heat Recovery Systems: Integrating heat exchangers to recover and reuse thermal energy from dryers and coolers.
- Biomass-Fired Boilers: Utilizing wood waste to generate process heat, reducing reliance on fossil fuels.
- Advanced Control and Monitoring Systems
To ensure compliance with environmental regulations, sophisticated control and monitoring systems are essential:- Continuous Emission Monitoring Systems (CEMS): Real-time monitoring of air emissions to ensure compliance with regulatory limits.
- Automated Process Control: Advanced PLC and SCADA systems optimize process efficiency and minimize environmental impact.
- Data Logging and Reporting: Comprehensive data collection and reporting capabilities to meet regulatory requirements for environmental performance documentation. (Related post: complete wood pellet plant for sale)
Raw Material Sourcing and Quality Control
Strict environmental regulations often extend to the sourcing of raw materials:
- Sustainable Forestry Certification: Production lines may need systems to track and verify the sustainability of wood sources.
- Contaminant Detection: Advanced screening and detection systems are necessary to remove non-wood materials and ensure pellet quality.
Facility Layout and Design
Environmental considerations influence the overall facility design:
- Buffer Zones: Increased setbacks from sensitive areas may be required, affecting the facility’s footprint and layout.
- Green Spaces: Integrating landscaping and green areas mitigates environmental impact and enhances aesthetics.
- Stormwater Management: Advanced collection and treatment systems are essential for protecting local water resources.
Case Study: Wood Pellet Production in Germany
Germany, known for its stringent environmental regulations, exemplifies how these requirements shape wood pellet production line design:
- Emission Control: Facilities often incorporate multi-stage emission control systems, including high-efficiency cyclones, baghouses, and RTOs, to meet TA Luft air quality standards.
- Energy Efficiency: The German Energy Saving Ordinance (EnEV) drives the implementation of energy-efficient technologies throughout the production line.
- Noise Control: Strict noise limits in residential areas necessitate comprehensive noise reduction measures in German wood pellet plants.
- Sustainable Sourcing: Regulations require detailed documentation of wood sources, influencing raw material handling and tracking systems in production lines.
Conclusion
Designing wood pellet production lines in countries with strict environmental protection requirements is a complex process that demands a holistic approach. Engineers and plant designers must consider a wide array of environmental factors, including air and water quality, noise pollution, and energy efficiency. While these stringent regulations present challenges, they also foster innovation in production technologies and practices.
As global environmental standards continue to evolve, the insights gained from designing wood pellet production lines in countries with strict regulations will likely influence industry practices worldwide. This trend toward environmentally conscious production methods not only ensures compliance with current regulations but also positions the wood pellet industry for long-term sustainability and social acceptance.