Two crucial components of the pellet equipment during the use are the roller as well as the die.
The relocating pellet maker suggests that the main shaft drives the level die to turn, as well as the stress roller does not move.The relocating roller pellet machine implies that the main shaft drives journalism roller to revolve, and also the flat die does stagnate. Relocating roll level die granulator for larger scale pellet manufacturing
Exactly How To Maintain Roller As Well As Die?
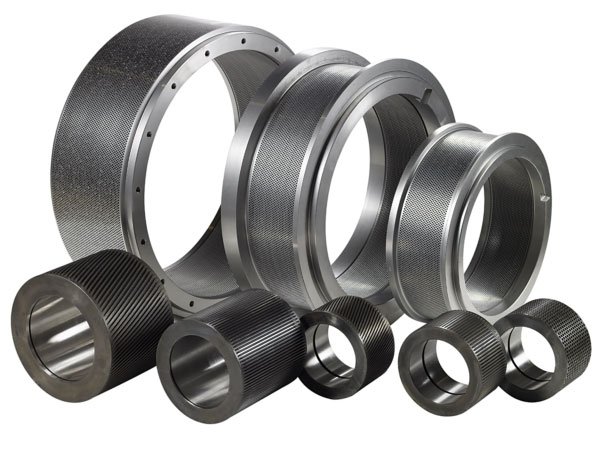
When acquiring a pellet machine, many individuals will certainly take into consideration whether it is power saving, dimension, comfort of motion, as well as price of pellet maker. As everybody understands, there is one more crucial point, that is, the devices of the feed granulation tools. According to customer comments, the expense of accessories each year accounts for nearly 8% of feed equipment costs.
Die and also rollers prevail putting on parts during using pellet feeders. When the individual surfaces utilizing it, it is best to acquire the raw product manufacturing facility accessories. The following describes some upkeep approaches for the die and the roller.
Consistently refuel the transmission parts of the biomass pellet maker, oil the roller bearings every 2 hours, and also oil the front bearings of the pin every 4 hrs to ensure flexible turning of the transmission parts of the pellet maker and reduce the working load.
Routinely replace the lubricating oil in the gearbox of the biomass pellet maker. After the new machine is run for half a month, the oil requires to be replaced when. After each continuous operation, it must be replaced as soon as for concerning 1000 hrs, which can extend the life span of the equipment.
Once a week, you must very carefully examine whether the connecting parts of each component hang, whether the safety and security switch is reliable, and tidy the feeding auger and conditioner to avoid mechanical failing.
Check the transmission secrets and also the wear of the hoops every half month, as well as if located the wear, they must be changed in time to stay clear of the ring mold and mildew drinking and affect the output.
Usage excellent quality ring mold and mildew, pressure roller. Inferior ring mold and mildews with rounded openings and harsh internal openings are removed, and the compression ratio of the ring mold is selected according to different formulas to guarantee smooth discharge of the ring mold, preventing raised power intake as well as lowering manufacturing ability.
Change the gap between the ring die and the press roller for each and every shift. If the equipment is obstructed, the pressure roller should be loosened to remove the material of the internal wall surface of the ring mold and mildew and then adjust the gap between the mold rolls. It has to not be required to begin, so regarding prevent damages to the transmission components and birthing components due to serious resonance.
To stop overload manufacturing. The manufacturing procedure can not surpass the functioning capacity of the biomass pellet equipment itself, otherwise the electric motor damages and also the accelerated wear of the components will certainly take place, shortening the life span of the pelletizer.
The raw materials must be cleaned as well as gotten rid of, and the iron removal tool need to be cleaned as soon as every shift to stop foreign matter from going into the ring mold and mildew functioning chamber, triggering the phenomenon of vibration and fracturing of the ring mold.
How To Decrease The Damages Of The Pellet Equipment?
The die of the pellet equipment ought to be flipped over with the opposite side after a time period. Don’t wait till the wear is significant, then turn it over. Particularly the thin die should be flipped often. It is not good to make use of both sides or your mold and mildew is pressed. If the fragments are not hard, they need to be processed and refurbished.
Die inspection and upkeep
Check the die before starting each time to guarantee that there are no foreign items on the grinding disc and also the die is not used. The service life of the die is 300-500 hrs under normal operating conditions. After the die is put on, the opposite side can be replaced (just one side of the die can be utilized).
Pressure roller inspection and also upkeep
Inspect the pressure roller prior to each startup to guarantee that no foreign matter hinders the roller from running easily, as well as check if the pressure roller is worn. The service life of the stress roller is 300-500 hrs under normal conditions. Normally, when the new die is changed, the stress roller shoule be replaced together.